Clasificación de los de los Materiales
Clasificación general de los de los Materiales
Contexto Histórico de los materiales
1. Edad de piedra (hasta ~3000 A.C.)- El hombre primitivo desarrolló una gran destreza para crear armas punzo-cortantes, tales como cuchillos, flechas y lanzas, para defenderse de las bestias.
- El hombre del neolítico descubrió que la arcilla (barro) se ablandaba al mezclarse con agua, y se endurecía al secarse. Este ciclo de ablandamiento-endurecimiento se podía repetir una y otra vez al ir añadiendo agua. Cuando se introducían los bloques de arcilla húmeda dentro de una hoguera por un determinado tiempo, éstos quedaban permanentemente endurecidos al enfriarse y eran resistentes al agua.
- Actuales Aplicaciones: En construcción (Puentes y edificios)

- El hombre neolítico descubrió que el cobre natural podía ser suavizado al calentarlo, y endurecido al deformarlo mediante martilleo.
- El cobre desplazó progresivamente a la piedra y se posicionó como el material preferido por el hombre para la fabricación de herramientas y objetos ceremoniales.
- Sin embargo, una vez que el cobre natural escaseó, el hombre se vio obligado a poner su atención en los metales contenidos en los minerales.
- Actuales Aplicaciones: Tendidos eléctricos, ornamentación, construcción, componentes de vehículo(radiadores, frenos), monedas.
- Los metales puros eran demasiado suaves para ser empleados como armas.
- Descubrieron que al mezclar mineral de estaño y mineral de cobre, previo al proceso de fundición, el producto resultante presentaba ventajas significativas en relación con todos los metales conocidos hasta entonces.
- El nuevo material era: – Más fácil de fundir que el cobre
- El hombre primitivo descubrió, desarrolló y perfeccionó las técnicas que permiten producir metales con propiedades sustancialmente diferentes a las de sus constituyentes individuales; es decir, inventó las aleaciones.
- Actuales Aplicaciones: Instrumentos musicales, Mecánica, Figuras decorativas, entre otras.
- “Hierro bueno” → Inventado accidentalmente por los hititas (Turquía)
- Se calentaba el hierro dentro de un horno de carbón, se martillaba la pieza para compactarla y se removía el óxido producido, repitiendo el procedimiento varias veces.
- Durante el calentamiento en el horno, los átomos de carbono se difundían hacia el interior del hierro, ¡produciendo acero de bajo carbono!
- Nunca se descubrió que el carbono era el responsable del “hierro bueno”, sino hasta 1774 d.C. (¡casi 3 mil años después!).
- Actuales Aplicaciones: Construcción, autos, barcos, edificios, entre otros.
- Mano del hombre desplazada por máquinas (construidas casi totalmente de hierro).
- La metalurgia cobró nuevos horizontes
- Desarrollo de medios de transporte (ferrocarril y barcos de vapor)
- El hierro y el acero se utilizaron en la construcción de puentes
- Se facilitaron las travesías comerciales entre las sociedades a lo largo de nuevos canales de navegación y carreteras.
- Descubrimiento de los rayos X y su aplicación
- Tabla periódica de los elementos
- Conocimiento de la estructura cristalina de los materiales
- Aparición de los primeros plásticos.
- Actuales Aplicaciones: Desarrollo de la industria del plásticos en todos sus tipos para el hogar, empresas y en general para todo tipo de necesidades.
Aleaciones Ferrosas
Diagrama Hierro Carbono
El hierro puro presenta alotropía, es decir cambia la estructura cristalina en función de la temperatura. Si vamos calentando desde la temperatura ambiente encontraremos las siguientes fases
- Hasta los 911 °C (temperatura crítica AC3), el hierro cristaliza en una estructura cúbica centrada en el cuerpo y recibe la denominación de hierro α (alfa) o ferrita. Esta es una solución sólida intersticial de carbono en una estructura cristalina BCC. Con una disolución máxima de carbono de 2.08% a 1148 °C. A temperatura ambiente se considera que disolución de carbono en ferrita es de 0.005% como máximo. Esta microestructura le concede al material propiedades como ductilidad y maleabilidad, y es responsable de la buena forjabilidad de las aleaciones con bajo contenido en carbono y es ferromagnético hasta los 770 °C (temperatura de Curie a la que pierde dicha cualidad; se suele llamar también AC2).
- Entre 911 y 1400 °C cristaliza en una estructura cúbica centrada en las caras y recibe la denominación de hierro γ (gamma) o austenita. Debido a que presenta mayor facilidad para que se muevan las dislocaciones la austenita se deforma con mayor facilidad y es paramagnética.
- Entre 1400 y 1538 °C cristaliza de nuevo en el «sistema cúbico centrado en el cuerpo» y recibe la denominación de hierro δ (delta), que es en esencia el mismo hierro alfa pero con un parámetro de red mayor por efecto de la temperatura.
A mayor temperatura, el hierro se encuentra en estado líquido.
Si se añade carbono al hierro, aumenta su grado de ductilidad y sus átomos podrían situarse simplemente en las posiciones intersticiales (los huecos que quedan entre los átomos de hierro); Cuando se adiciona más cantidad de la que es capaz de disolver, se forma un carburo de hierro (Fe3C), denominado cementita, de modo que casi todos los aceros aleados con carbono están formados realmente por ferrita y cementita.
Transformación de la austenita
El diagrama de fases Fe-C muestra dos composiciones singulares:
- Una mezcla eutéctica (composición para la cual el punto de fusión es mínimo) que se denomina ledeburita y que contiene un 4.3 de carbono (64,5% de cementita). La ledeburita aparece como uno de los constituyentes de la aleación cuando el contenido en carbono supera el 2% (región del diagrama no mostrada) y es la responsable de la mala forjabilidad de la aleación marcando la frontera entre los aceros con menos del 2% de C (forjables) y las fundiciones con porcentajes de carbono superiores (no forjables y fabricadas por moldeo). De este modo, se observa que, por encima de la temperatura crítica A3, los aceros están constituidos solo por austenita, una disolución sólida de carbono en hierro γ, y su microestructura en condiciones de enfriamiento lento dependerá por tanto de las transformaciones que sufra esta.
- Una mezcla eutectoide en la zona de los aceros equivalente al eutéctico pero en el estado sólido, donde la temperatura de transformación de la austenita es mínima. El eutectoide contiene un 0,80% de C (13,5% de cementita) y se denomina perlita. Está constituida por capas alternas de ferrita y cementita, siendo sus propiedades mecánicas intermedias entre las de ambas.
La existencia del eutectoide permite distinguir dos tipos de aleaciones de acero:
- Aceros hipoeutectoides (contenido de C menor de 0,80%). Al enfriarse por debajo de la temperatura crítica A3 comienza a precipitar la ferrita entre los granos de austenita y al alcanzar la temperatura crítica A1 la austenita restante se transforma en perlita. Se obtiene por tanto, a temperatura ambiente, una estructura de cristales de perlita embebidos en una matriz de ferrita.
- Aceros hipereutectoides (contenido de C mayor de 0,80%). Al enfriarse por debajo de la temperatura crítica precipita el carburo de hierro resultando a temperatura ambiente cristales de perlita embebidos en una matriz de cementita ya que este es un tratamiento térmico y su temperatura se eleva hasta dicha temperatura.
Las texturas básicas descritas (perlíticas) son las obtenidas enfriando lentamente aceros al carbono, sin embargo, modificando las condiciones de enfriamiento (base de los tratamientos térmicos) es posible obtener estructuras cristalinas diferentes:
- La martensita es el constituyente típico de los aceros templados y se obtiene de forma casi instantánea al enfriar rápidamente la austenita. Es una solución sobresaturada de carbono en hierro alfa con tendencia, cuanto mayor es la cantidad de carbono, a la sustitución de la estructura «cúbica centrada en el cuerpo» por «tetragonal centrada en el cuerpo». Tras la cementita (y los carburos de otros metales), es el constituyente más duro de los aceros.
- Las velocidades intermedias de enfriamiento dan lugar a la bainita, estructura similar a la perlita formada por agujas de ferrita y cementita pero de mayor ductilidad y resistencia que aquella.
- También se puede obtener austenita por enfriamiento rápido de aleaciones con elementos gammágenos (que favorecen la estabilidad del hierro γ) como el níquel y el manganeso; tal es el caso, por ejemplo, de los aceros inoxidables austeníticos.
Antaño se identificaron también la sorbita y la troostita que han resultado ser en realidad perlitas de muy pequeña distancia interlaminar por lo que dichas denominaciones han caído en desuso.
Aceros comunes y especiales.
Por otro lado, los aceros especiales incorporan aleaciones diseñadas para ofrecer propiedades específicas que los hacen idóneos para aplicaciones más exigentes.
Estas aleaciones pueden incluir elementos como cromo, níquel, molibdeno y vanadio, entre otros. Mejorando propiedades como la resistencia a la corrosión, la tenacidad y la conductividad térmica.
El coste de estos aceros es generalmente mayor, pero ofrecen características superiores que los hacen indispensables en ciertas industrias.
Encuentran su lugar en aplicaciones que demandan un rendimiento excepcional. Desde la fabricación de herramientas de corte de alta precisión hasta componentes para la industria aeroespacial, los aceros especiales se destacan en situaciones donde se requiere durabilidad y resistencia superior.
Clasificación y propiedades de los aceros especiales
Los diferentes aceros especiales se clasifican en función de sus propiedades y composición química. Estos incluyen:
- Aceros inoxidables: Se caracterizan por su alta resistencia a la corrosión, debido a la presencia de cromo en su aleación. Son ideales para condiciones ambientales agresivas o para el contacto con sustancias químicas.
- Aceros de herramientas: Estos aceros están optimizados para ser utilizados en la fabricación de herramientas de corte, moldes para plásticos y matrices. Presentan una excelente dureza y resistencia al desgaste.
- Aceros de alta velocidad: Diseñados para trabajar a altas temperaturas, como en el caso de herramientas que generan mucho calor por fricción.
- Aceros aleados: Los aceros aleados tienen cantidades específicas de diferentes elementos para proporcionar una variedad de propiedades, como una mayor dureza o resistencia al impacto.
- Aceros para trabajos en frío y en caliente: Estos se utilizan según el proceso de fabricación. Los aceros para trabajos en frío tienen alta resistencia al desgaste y a la deformación, mientras que los aceros para trabajos en caliente pueden soportar altas temperaturas sin perder tenacidad.
Clasificación norma SAE, AISI, ASTM.
Norma SAE
La clasificación SAE (Society of Automotive Engineers – EUA) es un sistema de identificación de 4 o 5 dígitos basada en la composición química del acero, es como un código que atesta cuales elementos están presentes en la aleación. Esta clasificación estandariza la composición del acero en todo el mundo y optimiza la producción que necesita de aleaciones específicas para cada demanda.
Justamente por ser una clasificación definida por ingenieros automotrices, es común encontrar otros insumos que utilizan el mesmo sistema, pero con composiciones diferentes – como el caso de los aceites automotrices que también son estandarizados por una clasificación SAE.
La misma clasificación también fue adoptada por la AISI (American Iron and Steel Institute). Ambos los organismos eran involucrados en la estandarización numérica del acero, pero, desde 1995, la AISI transfirió la manutención futura del sistema de clasificación para SAE, puesto que la AISI nunca llego a escribir ninguna de las especificaciones.
Este hecho es importante porque las certificaciones del acero comúnmente hacen referencia tanto al SAE cuanto al AISI y, para demandas más generalistas o trabajos manuales, no habrá diferencias entre trabajar con un acero denominado “SAE 4140” o “AISI 4140”. Aunque, para demandas más específicas, es recomendable seguir siempre la clasificación SAE exacta recomendada por los ingenieros.
Existen centenas de combinaciones de aleaciones de acero y por este motivo, la clasificación con números se torna la forma más fácil de identificar las propiedades de una composición.
El primer paso para interpretar la clasificación SAE es se quedar atento a las reglas de presentación en el formato ABXX o ABXXX. Los dos primeros dígitos identifican los elementos de la aleación existentes en el acero y sus contenidos, mientras los dos o tres dígitos finales indican los centésimos da porcentaje de C (Carbono) contenido en el material.
La cantidad de carbono puede oscilar entre 05 (equivalente a 0,05% de C) y 95 (equivalente a 0,95% de C). Caso este porcentaje ultrapase 1,00%, usamos 3 dígitos conforme la regla de redondeo decimal de la ABNT (Asociación Brasileña de Normas Técnicas) con apenas 2 números después de la coma. En el caso da clasificación SAE, la coma no existe, pero la interpretación es la misma.
Para identificar otros elementos en el acero, observamos los dos primeros dígitos (AB) en cifras decimales:
- AB = 10 – Acero al carbono simple
- AB = 20 – Acero – Níquell
- AB = 30 – Acero – Níquel – Cromo
- AB = 40 – Acero – Molibdenoo
- AB = 50 – Acero – Cromo
- AB = 60 – Acero – Cromo – Vanadio
- AB = 70 – Acero – Cromo – Tungsteno
- AB = 80 – Acero – Níquel – Cromo – Molibdeno
- AB = 92 – Acero – Silicio – Manganeso
- AB = 93,94,97 e 98 – Acero – Níquel – Cromo – Molibdeno
Esta es solamente una visión más básica y generalista para facilitar la interpretación, pero todo ingeniero posee acceso a una lista completa de los porcentajes de cada elemento contenido en la composición.
Norma AISI
AISI es el Instituto Americano del Hierro y Acero, conocido por sus siglas en Inglés American Iron and Steel Institute. Es la autoridad encargada de la designación y clasificación de los aceros inoxidables.
Fue fundada en 1855 para promover los intereses del comercio del acero en todas sus ramas. Desde tomar el control de calidad en las producciones de acero y brindándoles valores para identificarlos, hasta conseguir que la producción sea segura y respetuosa con el medio ambiente.
También, es fundamental mencionar a la organización SAE Sociedad de Ingenieros Automotores, por sus siglas en inglés Society of Automotive Engineers. Que conforma la norma AISI-SAE para la clasificación de los aceros y de materiales no ferrosos.
Se utiliza como una clasificación de los aceros inoxidables en las industrias, dependiendo de su aleación y componentes, distinguiéndose por utilizar un código de 3 dígitos con una o más letras.
El primer número se refiere al tipo de acero que se emplea, en el caso de los aceros al carbono el primer dígito es 1. También pueden incluirse prefijos, donde la “M” indica calidad corriente, “E” indica horno eléctrico, “H” indica endurecible.
Es de acuerdo a este valor que pueden ser reconocidos en el mercado y que sea posible elegir el tipo de acero adecuado para cada proyecto. Tomando en cuenta las propiedades y características de los aceros como son la templabilidad, ductilidad, maquinabilidad y dureza.
Clasificación de la norma AISI
El tipo 430 es el acero inoxidable más popular, además de ser fácil de formar, tiene una buena resistencia a la corrosión. Es de bajo contenido de carbono, contiene de 16 a 18% de cromo y un máximo de 0,12% de carbono. Se utiliza en materiales de construcción, molduras de automóviles, equipos químicos, e incluso en adornos arquitectónicos para interiores, entre otros.
El tipo 304 es conocido como acero inoxidable para todo propósito, por ser de alta calidad, moldeable y con una mayor resistencia a la corrosión. Es una aleación de hierro con un 18% de cromo y un 8% de níquel. Se emplea en equipos de cocina y hornos, al igual que en utensilios y elementos para la cocción de alimentos.
El tipo 1010 es de bajo contenido de carbono con un porcentaje de un 0,08% a 0,13% y hierro. Es un acero estructural que tiene alta ductilidad y excelente soldabilidad, se aplica para la formación primaria en productos forjados.
Es importante mencionar que la norma AISI-SAE reconoce nueve tipos de clasificación de los aceros, identificados con un dígito del 1 al 9. El primero indica el tipo de aleación base, el número posterior implica el elemento con el que se fusiona y los dos últimos determinan la cantidad de carbono que contiene el metal. Los números del primer dígito pueden ser lo siguiente:
- 1 carbono
- 2 níquel
- 3 níquel-cromo
- 4 molibdeno
- 5 cromo
- 6 cromo-vanadio
- 7 tungsteno-cobalto
- 8 níquel-cromo-molibdeno
- 9 manganeso-silicio
Norma ASTM
La reglamentación ASTM es la más popular internacionalmente para designar y regular la calidad de aceros de construcción y estructurales que comercialmente se ofrecen como productos terminados tales como: Barras de construcción corrugadas y lisas, perfiles estructurales, perfiles comerciales, placas y láminas.
En principio, la norma ASTM garantiza las propiedades mecánicas mínimas y la soldabilidad de los aceros, puesto que el uso de estos va orientado a la industria de la construcción y estructuras que requieran diversos materiales metálicos (para ser remachados, soldados o empernados).
Los estándares emitidos por la American Society for Testing and Materials, son designaciones sistemáticas fijas para cada tipo de acero con sus respectivas especificaciones y requerimientos para ser utilizados por los fabricantes y usuarios de los aceros.
Fundiciones.
Las fundiciones son aleaciones Fe-C-Si que contienen entre un 2 y un 4% de C y entre un 1 y un 3% de Si, y contenidos variables de otros elementos (Mn, P, S, etc.). Como los aceros, también se preparan fundiciones aleadas para conseguir mejores propiedades (alta resistencia a la abrasión y al desgaste, resistencia térmica y resistencia a la corrosión).
Las piezas de fundición son más fáciles de fabricar, más fáciles de mecanizar y son también más baratas que las de acero. Sin embargo, a diferencia de los aceros, las fundiciones de hierro no se trabajan en estado sólido sino que se obtienen directamente por colada a partir del metal fundido. Dado que las fundiciones no pueden distinguirse mediante un análisis químico, se clasifican en función de la distribución del carbono en sus microestructuras en cuatro tipos básicos:
Fundiciones blancas: en las que todo el carbono se encuentra como Fe3C, lo que le confiere gran fragilidad, y deben su nombre a que su superficie de fractura posee una tonalidad blanca. Las microestructuras de estas fundiciones se interpretan con el diagrama metaestable Fe-Fe3C. Al solidificar la fundición, aparece un microconstituyente, ausente en los aceros: ledeburita (agregado eutéctico formado por austenita saturada y Fe3C) que, a temperatura ambiente, se transforma en agrupaciones de Fe3C y perlita. Una alta velocidad de enfriamiento y un bajo carbono equivalente promueven la formación de la fundición blanca.
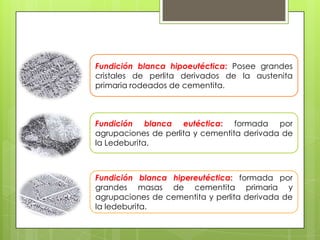
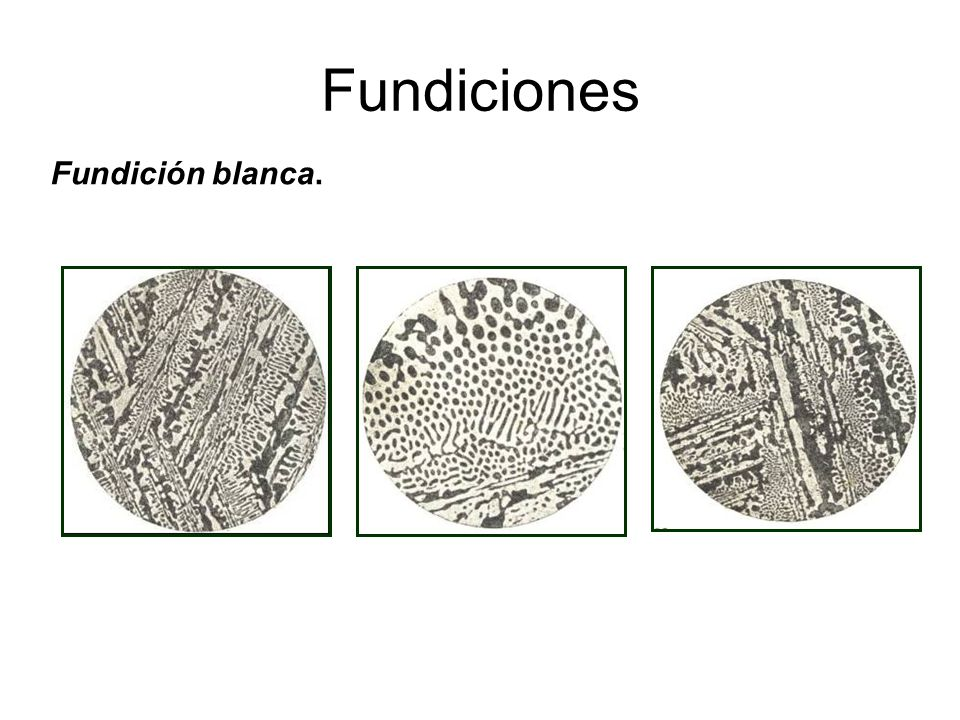
Fundiciones grises laminares: difieren de las fundiciones blancas en que en su microestructura, además de ferrita, Fe3C y perlita, aparece un nuevo microconstituyente, el grafito en forma de hojuelas, cuya formación se interpreta mediante el diagrama estable Fe-C. El silicio, que es un elemento grafitizante, está en mayor proporción en las fundiciones grises (1,5-3%) que en las fundiciones blancas (<1%). Además del silicio, la formación de grafito se favorece con una velocidad de enfriamiento lento durante la solidificación. Debido a sus propiedades (buena colada, excelente maquinabilidad, buena resistencia al desgaste y buena eliminación de vibraciones) y su bajo costo, son las fundiciones más empleadas para propósitos ingenieriles.
Fundiciones maleables: se obtienen a partir de la fundición blanca y por un proceso de recocido (maleabilización) que favorece la descomposición de la cementita en nódulos de grafito irregulares. Las propiedades mecánicas de la fundición varían en función del tratamiento térmico de recocido empleado. El espesor de las piezas está limitado por la necesidad de emplear una rápida velocidad de solidificación para obtener primeramente la fundición blanca.
Fundiciones dúctiles: en las que el carbono libre se encuentra en forma de grafito esferoidal tras la adición de pequeñas cantidades de Mg al hierro fundido antes de ser colado. A diferencia de las fundiciones maleables, pueden ser coladas tanto en piezas de pequeño como de gran tamaño. Su composición química es semejante a la de las fundiciones grises laminares, excepto que se requieren más bajos niveles de elementos minoritarios tales como S y P. Tienen un amplio margen de resistencias mecánicas junto con una razonable ductilidad.

Fundamentos de los tratamientos térmicos, Diagrama
TTT.
Tratamiento térmico del acero.
Los tratamientos térmicos de los aceros son numerosos y varían dependiendo del objetivo que se quiera conseguir con la pieza, en este sentido, a continuación te presentaremos los tratamientos más populares, mismos que permiten cambiar la estructura del metal para poder trabajarlo de una mejor manera y son los siguientes.
- Normalizado: Aquí la intención principal es que el acero regrese a un estado normal, liberándolo de tensiones internas que pudiese tener después de haber pasado por otros procesos en caliente o en frío.
- Tratamiento térmico recocido: En este proceso, se busca ablandar al acero, de este modo se podrá manipular de una mejor manera, además de incrementar sus propiedades mecánicas y eléctricas.
- Temple: El tratamiento térmico temple permite incrementar la fuerza del acero, durante este proceso se calienta la pieza en altas temperaturas y posteriormente se enfría de manera inmediata para obtener una mayor fuerza.
- Revenido: El revenido es un proceso complementario al del temple, pues solo se realiza en materiales previamente templados y con este proceso se busca mejorar la tenacidad y resiliencia del acero. Durante este trabajo, el acero se calienta a altas temperaturas para posteriormente dejarlo enfriar en agua o en aceite.
- Cementación: Logra endurecer la capa exterior del acero, lo que permite que el carbono penetre en el interior del mismo. El objetivo principal de este tratamiento es conseguir una mayor resistencia en la primera capa de la pieza.
- Bonificado: Durante este tratamiento, se logra darle al material que se está trabajando una mejor resistencia y tenacidad, sin embargo, a diferencia de los otros tratamientos térmicos para el acero, este metal podría adquirir una mayor elasticidad.
- Recocido: Finalmente, el objetivo de este procedimiento es lograr que el acero gane una mayor flexibilidad a costa de perder dureza. De esta forma, el material puede ser mecanizado, curado o reparado de mejor manera.
Templabilidad.
La templabilidad es la propiedad que determina la profundidad y distribución de la dureza inducida mediante el templado a partir de la condición austenitica.
Un acero aleado de alta templabilidad es aquel que endurece, o forma martensita, no sólo en la superficie sino también en su interior. Por tanto, la templabilidad es una medida de la profundidad a la cual una aleación específica puede endurecerse.
Hasta el momento se han discutido aspectos relativos al comportamiento del acero durante las diversas formas de transformación posibles en los mismos. Tanto los diagramas isotérmicos como los diagramas de enfriamiento continuo dan información valiosa al respecto de este comportamiento. Ellos indican, por ejemplo, que un acero puede ser enfriado más lentamente para obtener martensita cuando tiene elementos de aleación en su composición. Entretanto se debe considerar cual es realmente la información proporcionada por estos diagramas para efecto práctico en un tratamiento térmico. Se sabe que una pieza de acero enfriada en un medio cualquiera tendrá una velocidad de enfriamiento que depende de varios factores y una vez que estos son determinados, se debe buscar alguna manera de comparar y predecir lo que irá a suceder cuando se realice tal enfriamiento. Para esto es necesario que primeramente se entienda lo que es la templabilidad.
Ensayos Jominy.
El Ensayo Jominy es procedimiento estándar para determinar la templabilidad.
Se trata de templar una probeta estandarizada del acero estudiado. Primero se calienta a la temperatura de austenización, enfriándola posteriormente mediante un chorro de agua con una velocidad de flujo y a una temperatura especificada, el cual sólo enfría su cara inferior. Dicha cara actúa como superficie templante y enfría la probeta de forma longitudinal hacia su extremo superior solo por conducción, apareciendo un gradiente de velocidades de enfriamiento desde la máxima velocidad en el extremo templado (inferior), a la mínima en el extremo superior.
Una vez que la probeta se ha enfriado a temperatura ambiente, se desbasta una tira de 0,4 milímetros de espesor y se determina la dureza a lo largo de los 50 mm primeros de la probeta. En los primeros 12,5 mm las lecturas de dureza se toman a intervalos de 1,6 mm y en los 37,5 mm siguientes cada 3,2 mm. Después se traza una curva de templabilidad representando los valores de dureza en función de la distancia al extremo templado.
Aleaciones no ferrosas.
Los metales no ferrosos son aquellos metales y aleaciones que no contienen hierro en cantidades apreciables. Debido a sus propiedades, presentan ventajas específicas para varios procesos productivos, y resultan grandes aliados en la industria y construcción.
En general se diferencian de los metales ferrosos en ser más livianos, maleables, resistentes a la corrosión, y por su conductividad térmica y eléctrica. Otra de sus características distintivas consiste en ser metales no magnéticos.
Veamos con mayor detalle algunos metales no ferrosos y aleaciones de los mismos, de importancia esencial en diversas aplicaciones.
Aluminio
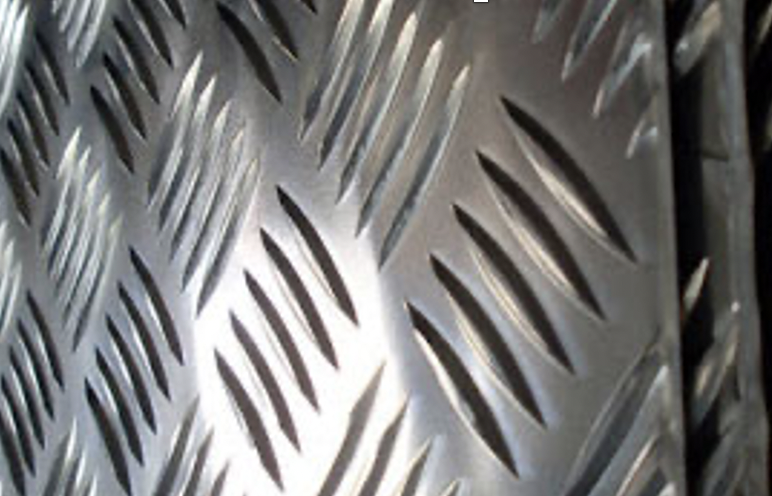
Debido a sus propiedades únicas, el aluminio es un material clave en muchas actividades productivas, industriales, y en la construcción. Por su menor densidad que el hierro, es vital si se necesita fuerza sin peso. Esta propiedad, así como su resistencia a la corrosión, lo hacen insustituible en procesos productivos de latas, envases, instrumentos, herramientas y partes fundamentales de variadas industrias, inclusive en sectores como la aeronáutica.
Bronce
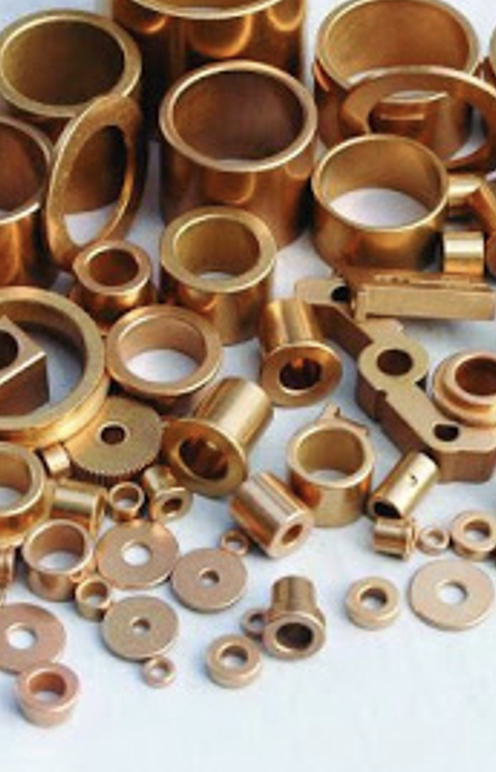
El bronce es la aleación de cobre y estaño. Por sus características anticorrosivas y resistencia al roce, es un material muy utilizado en la confección de determinados componentes de sistemas mecánicos.
Cobre
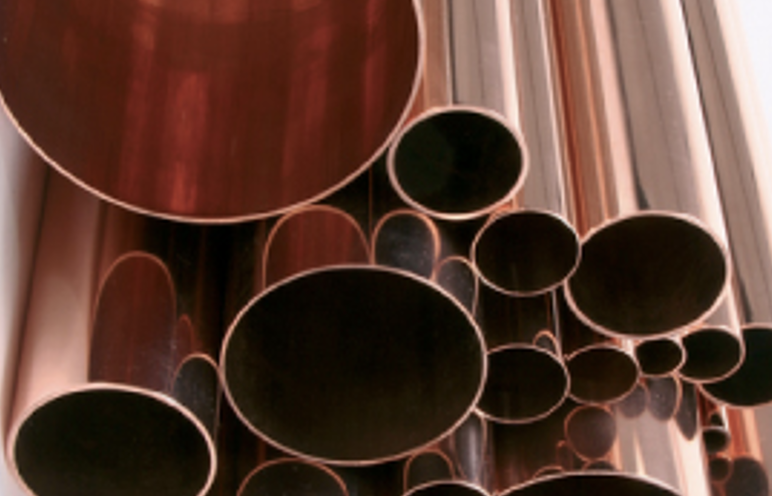
El cobre forma parte de aleaciones como el bronce y el latón, fundamentales en la historia de la humanidad y que siguen siendo importantes en la actualidad. Hoy en día se utiliza en la fabricación de cables eléctricos y componentes de la industria electrónica, grifería y tuberías domésticas e industriales, accesorios de cocina profesional.
Alpaca
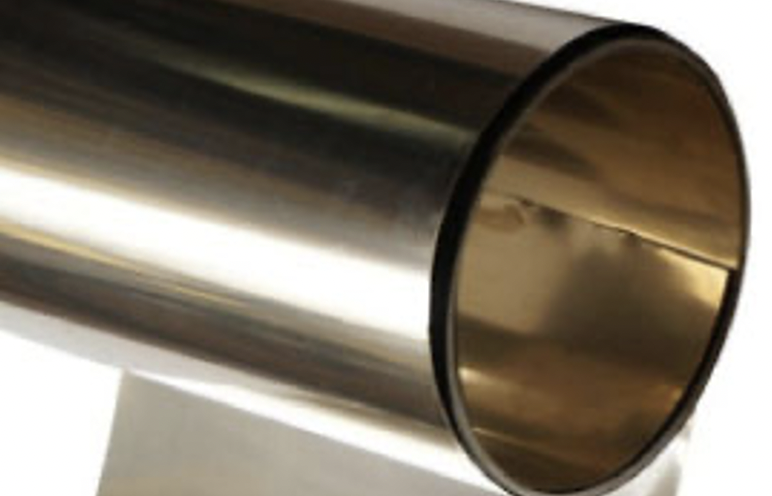
Es una aleación compuesta por níquel, cobre y zinc. Entre sus ventajas encontramos la resistencia a corrosión y oxidación, así como ser fácilmente trabajable a temperatura ambiente.
¿Cuáles son sus principales aplicaciones? Es muy utilizada en joyería, instrumentos quirúrgicos y dentales, partes de instrumentos musicales, vajilla y accesorios como bombillas de mate.
Estaño
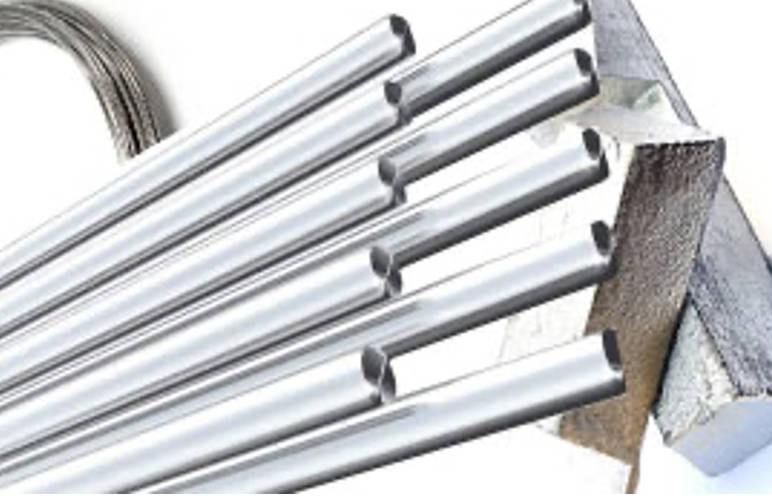
Utilizado para lograr aleaciones como el bronce, en soldadura blanda y en diversos recubrimientos antifricción, este metal es muy maleable, dúctil, anticorrosivo, y buen conductor eléctrico.
Plomo
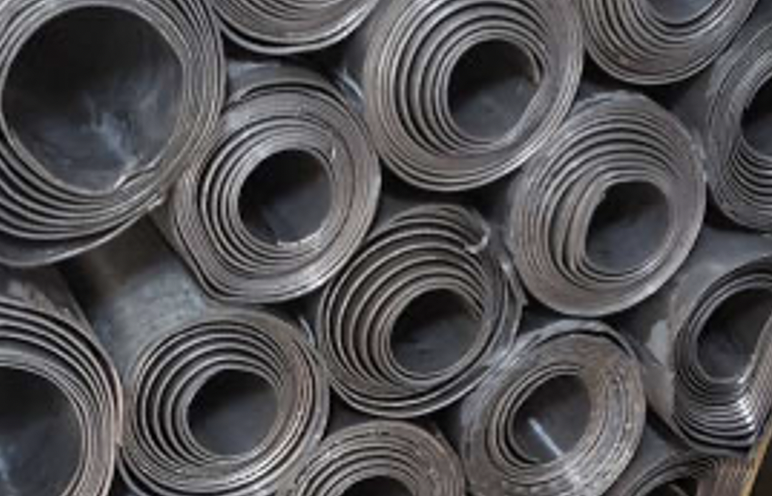
Metal de excelente resistencia a la corrosión, se funde con facilidad y se puede combinar en diversas aleaciones. Algunos de sus usos más importantes se dan en la producción de revestimientos, y placas protectoras contra rayos X.
Zinc
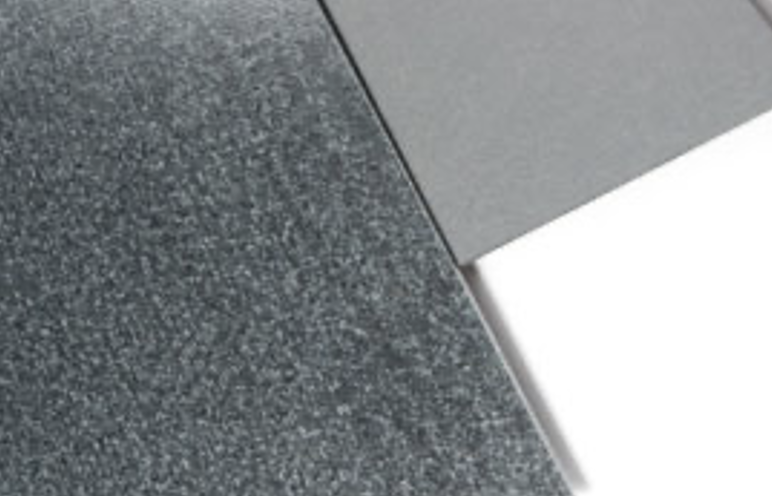
Lo encontramos principalmente en aleaciones y en el galvanizado de otros metales, como el acero, por la protección que brinda de la corrosión. Otras de sus aplicaciones incluyen las soldaduras blandas, baterías y componentes de computación, y láminas para revestimientos en la construcción.
Latón
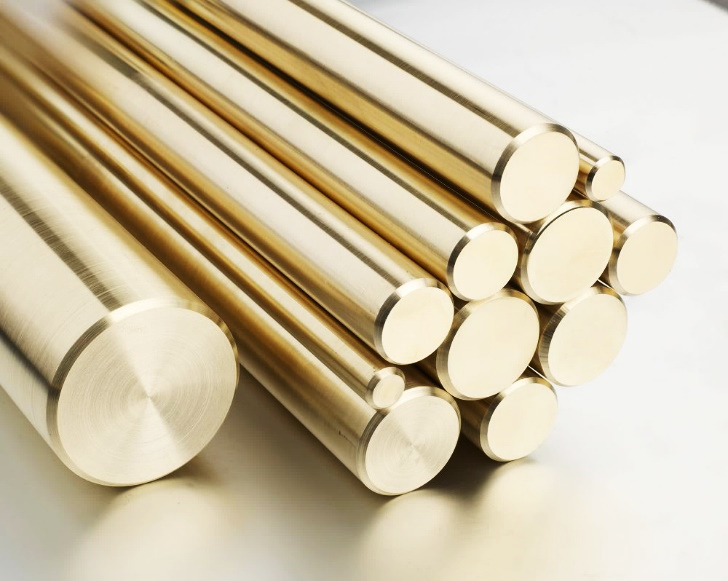
Aleación de cobre y zinc, que al igual que el bronce, es resistente al roce y a la corrosión. Esto lo hace ideal para la confección de partes mecánicas, instrumentos musicales, cerraduras, válvulas, piezas de fontanería.
Cobre y sus aleaciones.
¿Cuáles son las aleaciones del cobre ?
- El bronce: Es una aleación de cobre con estaño (Cu+Sn). El cobre supone un 75-80%. Actualmente el bronce se emplea en aleaciones conductoras de calor, en batería eléctricas, fabricación de llaves,.
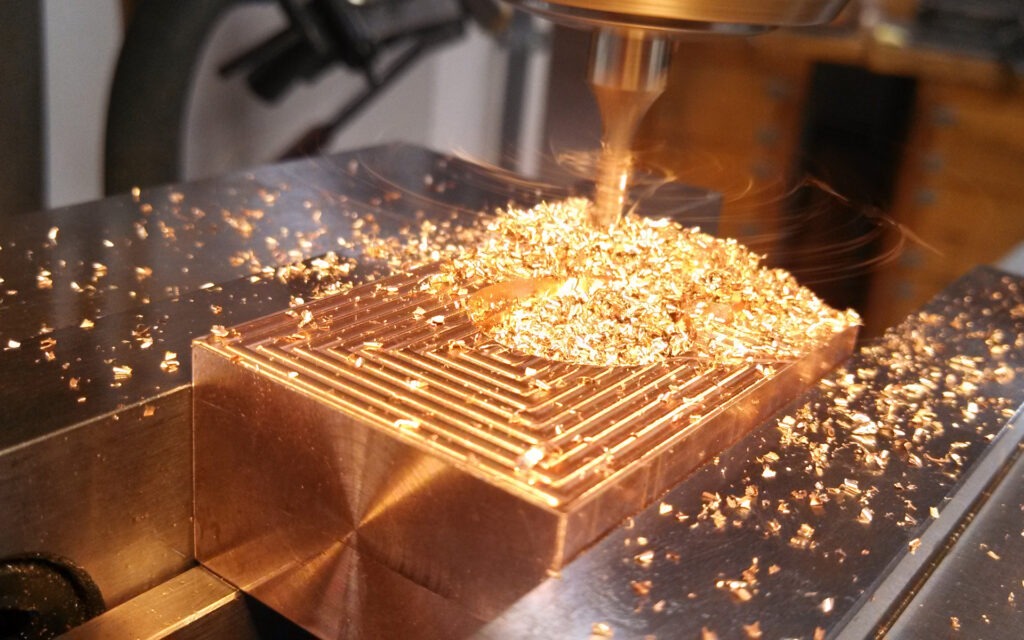
- Latones: Aleación de cobre con Zinc (Cu+Zn). El latón es más duro que el cobre, es resistente a la oxidación, a las condiciones salinas y es dúctil por lo que puede forjarse en planchas finas.
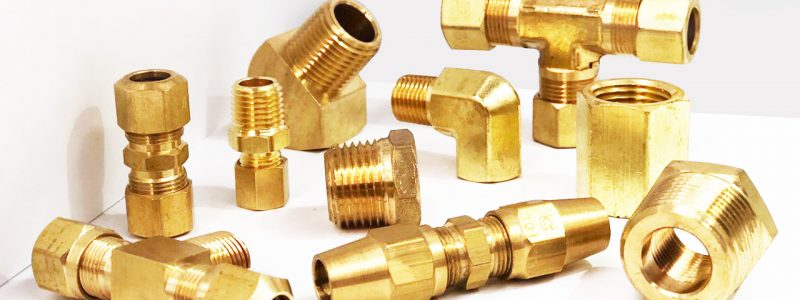
Aluminio y sus aleaciones.
Aleaciones de aluminio puro
A las aleaciones de este tipo también se le conocen como ALPUR. Están caracterizadas por presentar una elevada resistencia a los efectos producidos por agentes ambientales. De igual forma tienen una gran conductividad térmica y eléctrica y se adaptan de una manera bastante positiva a las deformaciones. Es un tipo de aleación utilizado en un sinnúmero de industrias, como la industria eléctrica, química, petroquímica, edificación, decoración, entre otros.
Aleaciones de aluminio-cobre
La función del cobre en este tipo de aleación es endurecer de manera significativa al aluminio, proporcionándole a esta unión propiedades mecánicas excepcionales, manteniendo en todo momento el excelente manejo físico y ligereza que determinan al mismo. De manera generalizada, este tipo de aleación se caracteriza por tener una buena resistencia al calor.
La desventaja principal que esta unión representa viene definida por la presencia del cobre, pues el mismo hace que esta combinación presente muy poca resistencia a los agentes atmosféricos. Este tipo de aleación solo puede ser soldada bajo técnicas especiales, como por ejemplo la soldadura por haz de electrón. Es importante resaltar que el porcentaje de cobre en este tipo de combinación comprende aproximadamente el 15% del producto total.
Aleaciones de aluminio-silicio
En esta aleación el porcentaje de silicio suele variar del 5% al 20%. Al igual que el cobre, el silicio endurece al aluminio, aumentando con esto su resistencia, pero además de lo mencionado, también aumenta la fluidez en la colada del material y proporciona una excelente resistencia a la corrosión. Las aleaciones de este tipo son muy dúctiles y presentan una gran resistencia al choque, teniendo además una elevada conductividad calorífica y eléctrica.
La principal aplicación de este tipo de aleación es la fundición de piezas difíciles, pero con buenas cualidades de moldeo, además de la fabricación de piezas para la marina debido a la gran resistencia a la corrosión que el material presenta. Es importante resaltar, que este tipo de combinación no se usa para la fabricación de piezas ornamentales, pues con el tiempo el mismo suele ennegrecerse.
Aleaciones de aluminio-cinc
En estas aleaciones el cinc se encuentra incorporado con un porcentaje máximo del 20% en el producto total. Las aleaciones de cinc, en comparación con las de cobre, son más económicas y proporcionan propiedades mecánicas iguales. La desventaja radica en que la aleación aluminio-cinc es menos resistente a la corrosión y son más pesadas.
Aleaciones de aluminio-magnesio
La presencia del magnesio en este tipo de combinación, comprende proporciones inferiores al 10%. De manera general, este tipo de aleación va asociado a otros elementos como el cobre, silicio, cinc, entre otros, formando de esta manera aleaciones ternarias, donde el papel del magnesio es el de menor proporción en la aleación total.
Las aleaciones aluminio-magnesio son más ligeras incluso que el propio aluminio en su estado puro. Posee buenas propiedades mecánicas y una alta resistencia a la corrosión.
Aleaciones de aluminio-manganeso
El manganeso es un elemento que se encuentra comúnmente en la mayor parte de las aleaciones de aluminio pero de formas ternarias y cuaternarias. De manera general, el manganeso ayuda a aumentar la dureza, la resistencia mecánica y el soporte a la corrosión de cualquier aleación de aluminio.
Las aleaciones de aluminio tienen cada día un mayor campo de aplicación, utilizándose en la fabricación de piezas que deben ser resistentes y ligeras al mismo tiempo. Su uso es cada vez más común en diferentes ámbitos de la creación industrial, comprendido desde las construcciones aeronáuticas, hasta la materialización de vagones de trenes y ferrocarriles.
Magnesio y sus aleaciones.
Los nombres de las aleaciones de magnesio a menudo se dan con dos letras seguidas de dos números. Las letras indican los principales elementos de aleación (A = aluminio, Z = zinc, M = manganeso, S = silicio). Los números indican las respectivas proporciones nominales de los principales elementos de la aleación. La denominación AZ91, por ejemplo, designa a una aleación de magnesio con aproximadamente una concentración en peso del 9 % de aluminio y del 1 % de zinc. La composición exacta debe confirmarse a partir de estándares de referencia.
El sistema de designación de las aleaciones de magnesio no está tan bien estandarizado como en el caso de los aceros o las aleaciones de aluminio; la mayoría de los productores siguen un sistema que usa una o dos letras de prefijo, dos o tres números y una letra de sufijo. Las letras del prefijo designan los dos principales metales de aleación de acuerdo con el siguiente formato desarrollado en la especificación B275 de la ASTM.
ASTM | B275 |
---|---|
A | Aluminio |
B | Bismuto |
C | Cobre |
D | Cadmio |
E | Tierras raras |
F | Hierro |
H | Torio |
J | Estroncio |
K | Zirconio |
L | Litio |
M | Manganeso |
N | Níquel |
P | Plomo |
Q | Plata |
R | Cromo |
S | Silicio |
T | Estaño |
V | Gadolinio |
W | Itrio |
X | Calcio |
Y | Antimonio |
Z | Zinc |
Titanio y sus aleaciones.
Las aleaciones de Ti destacan entre las aleaciones metálicas estructurales por su baja
densidad (4,42-4,76 g cm-3, ~45% inferior que la de los aceros), alta resistencia específica
(226-282 kN m kg-1) y excepcionalmente alta resistencia frente a la corrosión en la mayoría de los medios acuosos neutros y ácidos. Además son aptas para aplicaciones hasta una temperatura máxima de servicio de 600ºC.
El Ti puro existe en dos formas alotrópicas: fase α, hexagonal compacta (<882ºC), y fase β, cúbica centrada en el cuerpo (>882ºC). Los elementos aleantes en aleaciones de Ti se clasifican en α-estabilizadores (Al, O, N, C), β-isomorfos (V, Mo, Nb, Ta), β-eutectoides (Fe, Mn, Cr, Ni, Cu, Si, H) y neutros (Zr, Sn) en función de su efecto sobre los rangos de estabilidad de las fases α y β. Asimismo, en función de las fases presentes, las aleaciones se clasifican en α, α+β y β, con una utilización aproximada en el mercado del 26, 70 y 4% respectivamente. La aleación Ti-6Al-4V, siendo la más común de las aleaciones α+β, ocupa un 56% del mercado total del Ti debido a un equilibrio excepcional entre resistencia mecánica, ductilidad, resistencia a fatiga y tenacidad de fractura y que se mantiene hasta 300ºC.
Las propiedades mecánicas de las aleaciones α+β tienen una relación compleja con el contenido de soluto β-isomorfo y el tipo de tratamiento térmico (temple, recocido, revenido o envejecimiento). Como se verá en esta sección, las microestructuras resultantes ( y por tanto las propiedades mecánicas) vienen determinadas por la transformación de fase β y que a su vez depende de la velocidad de enfriamiento.
Metales refractarios.

Super aleaciones.
Las superaleaciones ofrecen una excelente resistencia mecánica, además de brindar una gran resistencia a altas temperaturas, estabilidad y una gran resistencia a la corrosión y la oxidación. Principalmente es usado para el sector aeroespacial, así como válvulas bi-metálicas, por donde circulan ácidos altamente corrosivos.
Las superaleaciones tienen una matriz austenítica y un elemento de superaleación de base de aleación es generalmente níquel, cobalto o níquel-hierro. Algunos ejemplos de superaleaciones son Hastelloy, Inconel, Waspaloy, aleaciones René, aleaciones de Haynes ó Incoloy.
Otra característica importante de las superaleaciones es la resistencia a la fatiga, es por ello que se usa en gran medida a la industria aeroespacial.
Las superaleaciones pueden ofrecer resistencia a altas temperaturas gracias a su fortalecimiento de solución sólida. La oxidación y resistencia a la corrosión es proporcionada por la formación de un recubrimiento de barrera térmica, que se forma cuando el metal está expuesto al oxígeno y recubre el material.
También se utilizan en medios corrosivos en lugar de otros materiales metálicos (por ejemplo) en lugar de acero inoxidable en ambientes de agua salada o ácido.
Las superaleaciones basadas en níquel, como regla general, poseen una composición química compleja. Incluye de 12 a 13 componentes cuidadosamente equilibrados para obtener las propiedades requeridas. El contenido de impurezas tales como silicio (Si), fósforo (P), azufre (S), oxígeno (O) y nitrógeno (N) también está controlado. El contenido de elementos tales como selenio (Se), teluro (Te), plomo (Pb) y bismuto (Bi), debe ser insignificante, siempre que la selección de materias primas con un contenido bajo de estos elementos, pues no es posible deshacerse de ellos durante la fusión. Estas aleaciones contienen normalmente de un 10 a 12% de cromo (Cr), hasta un 8% de aluminio (Al) y titanio (Ti), de 5 a 10% de cobalto (Co), así como pequeñas cantidades de boro (B), circonio (Zr) y carbono (C). A veces, el agregado de molibdeno (Mo), wolframio (W), niobio (Nb), tántalo (Ta) y hafnio (Hf).
La otra vertiente de superaleaciones, son quellas basadas en cobalto son aleaciones se denominan "estelite", se utilizan para la producción de herramientas de corte y piezas resistentes al desgaste. A pesar de que las superaleaciones basadas en niquel desplazaron a las aleaciones basadas en cobalto, existen muchas aplicaciones ideoneas para continuar con las aleaciones basadas en níquel.
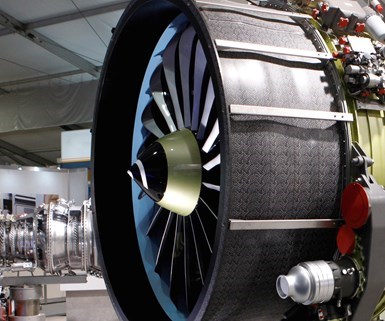
Corrosión.
La corrosión se define como el deterioro de un material a consecuencia de un ataque electroquímico por parte de su entorno. De manera más general, puede entenderse como la tendencia general que tienen los materiales a buscar su forma de mayor estabilidad o de menor energía interna. Siempre que la corrosión esté originada por una reacción electroquímica (oxidación), la velocidad a la que tiene lugar dependerá en alguna medida de la temperatura, de la salinidad del fluido en contacto con el metal y de las propiedades de los metales en cuestión. Otros materiales no metálicos también sufren corrosión mediante otros mecanismos. El proceso de corrosión es natural y espontáneo.
La corrosión es una reacción química (óxido-reducción) en la que intervienen tres factores: la pieza manufacturada, el ambiente y el agua, o por medio de una reacción electroquímica.
Los factores más conocidos son las alteraciones químicas de los metales a causa del aire, como la herrumbre del hierro y el acero o la formación de pátina verde en el cobre y sus aleaciones (bronce, latón).
Es un problema industrial importante, pues puede causar accidentes (ruptura de una pieza) y, además, representa un costo importante, ya que se calcula que cada pocos segundos se disuelven cinco toneladas de acero en el mundo, procedentes de unos cuantos nanómetros o picómetros, invisibles en cada pieza pero que, multiplicados por la cantidad de acero que existe en el mundo, constituyen una cantidad importante.

Comportamiento elástico y plástico
Comportamiento Elástico.
Cuando se somete una pieza de metal, o de otro tipo de material, a una fuerza de tracción uniaxial se produce la deformación del metal. Si el material recupera sus dimensiones originales cuando se elimina la fuerza, se considera que el metal ha sufrido una deformación elástica. Cuando se retira la carga el material recupera su forma original.
La mayoría de los materiales, cuando se someten a un nivel bajo de carga, se comportan de manera lineal elástica. Es decir, el alargamiento del material es directamente proporcional al nivel de carga aplicado - la gráfica tensión versus deformación es una línea recta. Este comportamiento se conoce como la Ley de Hooke.
La ley de Hooke indica que la relación entre la deformación producida y la tensión que la provoca es lineal. La pendiente de la recta tensión/deformación se denomina Módulo de Young, o módulo de elasticidad, E.
Comportamiento plástico.
La plasticidad es un comportamiento mecánico característico de ciertos materiales inelásticos consistente en la capacidad de deformarse permanente e irreversiblemente cuando se encuentra sometido a tensiones por encima de su rango elástico, es decir, por encima de su límite elástico.
En los metales, la plasticidad se explica en términos de desplazamientos irreversibles de dislocaciones.
La plasticidad de los materiales está relacionada con cambios irreversibles en esos materiales. A diferencia del comportamiento elástico que es termodinámicamente reversible, un cuerpo que se deforma plásticamente experimenta cambios de entropía, como desplazamientos de las dislocaciones. En el comportamiento plástico parte de la energía mecánica se disipa internamente, en lugar de transformarse en energía potencial elástica.
Comportamiento elástico a nivel atómico
Base Físicas del módulo de elasticidad
El módulo de elasticidad de un material es una medida de su rigidez. Para probar esto, se aplica fuerza al material y se registran los resultados. Entonces es posible calcular el módulo de elasticidad como igual a la tensión aplicada al material dividida por la deformación elástica resultante.
Deformación Plástica para deslizamiento
En ciencia de materiales, deslizamiento es el proceso por el cual se produce deformación plástica por el movimiento de dislocaciones. Debido a una fuerza externa, partes de la red cristalina se deslizan respecto a otras, resultando en un cambio en la geometría del material. Dependiendo del tipo de red, diferentes sistemas de deslizamiento están presentes en el material. Más específicamente, el deslizamiento ocurre entre los planos que tienen el menor vector de Burgers, con una gran densidad atómica y separación interplanar.
Sistema de Deslizamiento en algunas estructuras cristalinas
La deformación plástica se da únicamente en los metales debido a que son enlaces en los cuales los electrones se comparten entre todos los átomos participantes, de manera deslocalizada. En enlaces iónicos o covalentes este deslizamiento de las dislocaciones no puede tener lugar.
El deslizamiento de las dislocaciones no sigue direcciones al azar. Las dislocaciones de cuña, cuando se les aplica una fuerza suficiente, se deslizan a través de la red en una dirección perpendicular a la dislocación. Las dislocaciones helicoidales se deslizan en una dirección paralela a la línea de dislocación. Si se tiene una dislocación mixta, ambas direcciones son la misma.
Además, las direcciones de deslizamiento de las dislocaciones siempre tienen lugar en planos de empaquetamiento compacto de la red cristalina, y dentro de estos planos, en direcciones de empaquetamiento compacto. Ello se debe a que en esos planos y direcciones las dislocaciones pueden moverse con la mínima distorsión atómica. El conjunto de planos y direcciones compactas de la red cristalina se denomina SISTEMA DE DESLIZAMIENTO.
Las direcciones de deslizamiento son siempre las de mayor densidad lineal de átomos: direcciones compactas donde los átomos se tocan unos a otros.Los planos de deslizamiento son siempre los de mayor densidad planar de átomos (los más compactos)
Cuanto mayor es el número de sistemas de deslizamiento, más dúctil es el material: Mayor deformación podrá soportar antes de romperse.
Esfuerzos constantes críticos
En el contexto de la elasticidad y la plasticidad de los materiales, los esfuerzos críticos son valores límite que determinan el comportamiento del material bajo carga. Estos esfuerzos críticos son puntos de referencia importantes que ayudan a comprender cómo un material se comporta cuando se somete a fuerzas externas.
Esfuerzo crítico en elasticidad: En elasticidad, el esfuerzo crítico se refiere al límite elástico del material, que es la máxima cantidad de esfuerzo que un material puede soportar sin experimentar una deformación permanente. Más allá del límite elástico, el material puede deformarse de manera permanente, pero dentro de este límite, el material se comporta de manera elástica, es decir, vuelve a su forma original una vez que se elimina la carga. Este esfuerzo crítico es importante para determinar la seguridad y la durabilidad de las estructuras y componentes.
Esfuerzo crítico en plasticidad: En plasticidad, el esfuerzo crítico se refiere al límite de fluencia del material, que es la máxima cantidad de esfuerzo que un material puede soportar antes de comenzar a fluir o deformarse de manera permanente. Una vez que se supera el límite de fluencia, el material experimenta deformaciones permanentes incluso después de que se retire la carga. Este esfuerzo crítico es fundamental en el diseño de estructuras y componentes que experimentan cargas cíclicas o cargas que exceden el límite elástico del material.
Fractura y tipos de fractura
En elasticidad y plasticidad, la fractura se refiere a la separación o ruptura de un material debido a la aplicación de fuerzas externas. La fractura puede ocurrir tanto en materiales elásticos como plásticos, pero las características y los mecanismos de fractura pueden ser diferentes en cada caso. Aquí hay una descripción de los tipos de fractura en elasticidad y plasticidad:
Fractura en elasticidad:
Fractura frágil: En la fractura frágil, el material se rompe de manera repentina y sin deformación significativa antes de la fractura. Este tipo de fractura es típico en materiales frágiles como el vidrio, la cerámica y ciertos metales a bajas temperaturas. La fractura frágil es causada generalmente por defectos en la estructura del material, como grietas preexistentes o discontinuidades.
Fractura dúctil: La fractura dúctil implica una deformación significativa del material antes de la ruptura. El material experimenta una deformación plástica considerable antes de que se forme la fractura. Este tipo de fractura es común en materiales dúctiles como el acero a temperaturas moderadas. La fractura dúctil puede ser precedida por la formación y el crecimiento de cavidades internas, seguido de la coalescencia de estas cavidades para formar una fisura que eventualmente conduce a la fractura final.
Fractura en plasticidad:
Fluencia y estricción: En materiales plásticos, la fractura puede estar precedida por un fenómeno llamado fluencia, donde el material se deforma continuamente bajo cargas constantes o cíclicas. Durante la fluencia, el material experimenta estricción, que es la reducción de su sección transversal debido a la deformación. Este proceso puede continuar hasta que el material alcanza su límite de fluencia y finalmente se fractura.
Fatiga y fractura por fatiga: La fractura por fatiga ocurre en materiales que están sujetos a cargas cíclicas repetidas. Con el tiempo, las fluctuaciones en las cargas pueden provocar la formación y propagación de grietas en el material, que eventualmente conducen a la fractura. Este tipo de fractura es común en aplicaciones donde los materiales están sujetos a cargas variables, como en componentes mecánicos y estructurales.
Endurecimiento
En metalurgia, el endurecimiento se refiere a técnicas para incrementar la dureza de un material. Existen cinco mecanismos principales para hacer esto:
- Endurecimiento por la agregación de partículas de segunda fase.
- Endurecimiento por afino de grano.
- Endurecimiento por deformación en frío.
- Endurecimiento por solución sólida.
- Endurecimiento por precipitación y dispersión.
- Transformaciones martensíticas.
Todos los mecanismos de endurecimiento, excepto las transformaciones martensíticas, introducen dislocaciones o defectos en la estructura cristalina, las cuales actúan como barreras para los deslizamientos.
Introducción
El endurecimiento es un proceso metalúrgico para aumentar la dureza de los metales por transformación térmica (enfriamiento y templado), tensión inducida mecánicamente (endurecimiento por deformación), precipitación (mediante tratamiento térmico y posterior envejecimiento), fortalecimiento de la solución sólida (por ejemplo, carburación) o reducción del tamaño de grano del material.
Todos los métodos de endurecimiento se caracterizan por el aumento de los defectos o dislocaciones de la estructura cristalina.
Endurecimiento por solución sólida
Endurecimiento por disolución sólida: este método se basa en introducir en los materiales átomos en forma de impurezas que se disuelven en solución sólida sustitucional o intersticial. Estos átomos dificultan el movimiento de las dislocaciones evitando que avancen, por tanto, endureciendo el material.
Por precipitación y dispersión
Por precipitación
El endurecimiento por precipitación es un proceso de tratamiento térmico utilizado para aumentar el límite elástico de la mayoría de las aleaciones y de algunos aceros y aceros inoxidables. Se basa en la deposición de fases metaestables en forma finamente dividida, de modo que forma una barrera eficaz contra los movimientos de las dislocaciones. La resistencia a la fluencia de las aleaciones así tratadas puede aumentar hasta 300 MPa.
Por dispersión
El endurecimiento comprende las diferentes técnicas que se utilizan para aumentar la resistencia de un material a ser rayado o penetrado por otro material con morfología y durezas diferentes a las del sustrato.En la técnica de Endurecimiento por Dispersión se introducen elementos de una fase, que por lo general es más dura y densa, sobre otra fase, la matriz, que es menos dura, pero a su vez más dúctil.
El concepto de dispersión se da por la manera en que fueron adicionados los elementos de la fase dura sobre la matriz.
La criticidad de este proceso está en adicionar elementos muy pequeños y dispersos como fase dura. De esta manera, se realizará un bloqueo en las dislocaciones ocurridas en la matriz en el momento de conformación. Así, permitirá que mediante un cambio de fase se logre el endurecimiento.
A más cantidad de elementos o partículas de menor tamaño, nanométricas y de geometrías redondas, el endurecimiento será mayor. En ese sentido, habrá más bloqueos a los movimientos de la matriz. Perderá ductilidad, pero ganará dureza.
Por deformación
El endurecimiento por deformación (también llamado endurecimiento en frío o por acritud) es el endurecimiento de un material por una deformación plástica a nivel macroscópico que tiene el efecto de incrementar la densidad de dislocaciones del material. A medida que el material se satura con nuevas dislocaciones, se crea una resistencia a la formación de nuevas dislocaciones y a su movimiento. Esta resistencia a la formación y movimiento de las dislocaciones se manifiesta a nivel macroscópico como una resistencia a la deformación plástica.
En cristales metálicos, el movimiento de las dislocaciones es lo que produce la deformación plástica (irreversible) a medida que se propagan por la estructura del cristal. A temperaturas normales cuando se deforma un material también se crean dislocaciones, en mayor número de las que se aniquilan, y provocan tensiones en el material, que impiden a otras dislocaciones el libre movimiento de estas. Esto lleva a un incremento en la resistencia del material y a la consecuente disminución en la ductilidad.
Por límites de grado y por fibra
Endurecimiento por límites de grano:
Proceso: En el endurecimiento por límites de grano, se aprovecha la presencia de límites de grano en la estructura policristalina del material. Estos límites de grano son interfaces entre los granos individuales en el material. Al manipular la estructura de grano, se puede aumentar la resistencia del material.
Mecanismo: La presencia de límites de grano actúa como obstáculos para el movimiento de dislocaciones dentro del material. Cuanto más finos sean los granos, más límites de grano habrá, y más efectivo será este mecanismo de endurecimiento. Además, la presencia de impurezas segregadas a lo largo de los límites de grano puede ayudar a reforzar aún más el material.
Endurecimiento por fibra:
Proceso: En el endurecimiento por fibra, se introducen fibras o alambres finos y resistentes dentro de la matriz del material. Estas fibras pueden estar hechas de materiales como carburos, óxidos o cerámicas.
Mecanismo: Las fibras proporcionan una resistencia adicional al material al servir como obstáculos físicos para el movimiento de dislocaciones. Las dislocaciones se deforman alrededor de las fibras, lo que aumenta la resistencia y la tenacidad del material.
Propiedades mecánicas
Las propiedades mecánicas de un material son aquellas que afectan a la resistencia mecánica y a su capacidad cuando se les aplica una fuerza. Es decir, las propiedades mecánicas son aquellas que posee un material relacionadas con sus posibilidades de transmitir y resistir fuerzas o deformaciones.
Estas propiedades resultan de suma importancia, ya que aquellos materiales destinados a productos de ingeniería deben tener una resistencia mecánica óptima para ser capaces de trabajar bajo diferentes fuerzas o cargas.
Principales propiedades mecánicas
Dentro de este campo existen multitud de propiedades que se pueden medir. Algunas de las más comunes son las siguientes:
Resistencia: Se opone a la deformación o ruptura del material en presencia de fuerzas o cargas externas.
Tenacidad: Es la capacidad de un material para absorber la energía y deformarse plásticamente sin fracturarse.
Dureza: Es la capacidad para resistir el cambio de forma permanente debido a la tensión externa.
Fragilidad: Indica la facilidad con la que se fractura un material cuando se somete a una fuerza o carga.
Maleabilidad: La facilidad con la que un material se deforma bajo tensión de compresión en forma de lámina.
Ductilidad: Es la deformación bajo tensión de un material. La mayoría de los aceros comunes son bastante dúctiles y pueden soportar concentraciones locales de tensión. En cambio, los materiales frágiles, como el vidrio, no pueden soportar concentraciones de tensión porque carecen de ductilidad y se fracturan fácilmente.
Fluencia: La tendencia del material a moverse lentamente y a deformarse permanentemente bajo la influencia de una tensión mecánica externa.
Resiliencia: Es la capacidad que posee el material de absorber la energía cuando se deforma elásticamente aplicando una tensión y liberar la energía cuando se elimina la tensión. La resiliencia probada se define como la energía máxima que puede ser absorbida sin que se produzca una deformación permanente.
Fatiga: Se trata del debilitamiento del material causado por la carga repetida del mismo. Cuando un material se somete a cargas cíclicas y a cargas superiores a un determinado valor umbral, pero muy por debajo de la resistencia del material, límite de resistencia a la tracción o límite de fluencia, comienzan a formarse grietas microscópicas en los límites del grano y en las interfaces. Finalmente, la grieta alcanza un tamaño crítico. Esta grieta se propaga repentinamente y la estructura se fractura.
Comportamiento tensión- deformación
Para una misma tensión se deforman menos (son más rígidos) si la carga se aplica a gran velocidad (por ejemplo un impacto) que si la carga es aplicada lentamente. Es decir, su elasticidad varía con la velocidad de aplicación de la fuerza.
Deformación elástica, Propiedades elásticas
Cuando un material se somete a una tensión, sufre una deformación elástica, lo que significa que cambia temporalmente de forma. Sin embargo, una vez que se elimina la fuerza, el material vuelve a su forma original, mostrando sus propiedades elásticas.
Un ejemplo clásico de deformación elástica es el estiramiento de una banda elástica. Cuando se estira, la banda elástica se alarga, pero recupera su forma original cuando se suelta. Este comportamiento se debe a las propiedades elásticas del material de caucho, lo que le permite sufrir deformaciones temporales sin daños permanentes.
Deformación plástica fluencia y límite elástica, ductilidad, fragilidad, resiliencia
Deformación plástica fluencia
La fluencia es la pérdida de estabilidad dimensional (deformación plástica) que se produce en algunos materiales cuando las tenciones aplicadas crecen por encima de un determinado valor, denominado límite de fluencia.
Límite elástica
El límite elástico es una especie de límite de fluencia sustitutivo. Se utiliza principalmente para materiales que no tienen un límite de fluencia pronunciado. Debido a la transición continua entre las zonas elástica y plástica del material, el límite de fluencia no puede medirse de forma inequívoca.
Ductilidad
La ductilidad es una propiedad que presentan algunos materiales, como las aleaciones metálicas o materiales asfálticos, los cuales bajo la acción de una fuerza, pueden deformarse plásticamente de manera sostenible sin romperse, permitiendo obtener alambres o hilos de dicho material. A los materiales que presentan esta propiedad se les denomina dúctiles. Los materiales no dúctiles se califican como frágiles. Aunque los materiales dúctiles también pueden llegar a romperse bajo el esfuerzo adecuado, esta rotura solo sucede tras producirse grandes deformaciones.
Algunos ejemplos de materiales muy dúctiles son el oro, la plata, el cobre, el bronce y el latón.
En otros términos, un material es dúctil cuando la relación entre el alargamiento longitudinal producido por una tracción y la disminución de la sección transversal es muy elevada.
Fragilidad
La fragilidad es un síndrome geriátrico previo a la aparición de la dependencia funcional, que permite la identificación de individuos de mayor riesgo de dependencia, institucionalización, efectos adversos de fármacos, mortalidad y otros eventos negativos de salud.
Resiliencia
La resiliencia significa ser capaz de afrontar eventos difíciles. Cuando pasa algo malo, sientes ira, sufrimiento y dolor. Sin embargo, puedes seguir adelante, tanto física como psicológicamente. La resiliencia no significa tolerar una situación difícil ni afrontarla tú solo.
Tenacidad, Recuperación elástica
Tenacidad
Sustantivo femenino. La propiedad y cualidad de ser tenaz, persistente o firme, o de sostenerse o pegarse fuertemente. Sinónimos: persistencia, fortaleza, determinación. Antónimos: desidia, pusilanimidad, debilidad, falta de carácter.
Recuperación elástica
La recuperación elástica se puede definir como un cambio elástico que ocurre en un elemento deformado durante la eliminación de las cargas externas. Siendo un fenómeno físico complejo que se rige principalmente por el estado de tensión obtenido al final de la deformación.
Tensión y deformaciones reales. Dureza
Tensión y deformaciones reales.
El ensayo de tracción simple uniaxial (UNE-EN 10080) es quizás el más importante para determinar el comportamiento mecánico y resistente de un material isótropo ante tensiones de tracción, y nos da una clara idea de los dominios de deformación del mismo a lo largo de sus estadios de tensión. El grafo trazado con los valores obtenidos de este ensayo se denomina Diagrama Tensión – Deformación real, y es característico de cada material. Está dividido en varias etapas según el comportamiento del material, no existiendo todas las etapas en todos los materiales.

La idealización del diagrama real motivado por criterios de economía de cálculo y aprovechamiento del material, resultará en el Modelo Constitutivo del material, que determinará la hipótesis básica de su respuesta elástica. Los modelos constitutivos los establece cada normativa como base de la formulación desarrollada.
Dureza se refiere a aquello que es duro, resistente y que carece de flexibilidad.
La dureza es el obstáculo o impedimento que presentan algunos materiales cuando se desea alterar su condición física debido a la cohesión de sus átomos. Es decir, es difícil de rayar, penetrar, desgastar, romper, deformar o abrasar.
Por ejemplo, el metal es un material que tiene una gran dureza en comparación al plástico.Generalmente, dureza es un término que se acostumbra a usar en mineralogía y geología para referirse a la dureza y el grado de resistencia que posee un mineral al ser rayado o penetrado por otro material.
Ensayos mecánicos
Los ensayos mecánicos permiten conocer algunas de las propiedades mecánicas, así como el estado microestructural de diferentes materiales metálicos sin tener que destruir las muestras, ni desmontarlas y enviarlas a un laboratorio.
Ensayos de tracción y compresión
Ensayos de tracción
El ensayo de tracción de un material consiste en someter a una probeta normalizada a un esfuerzo axial de tracción creciente hasta que se produce la rotura de la misma. Este ensayo mide la resistencia de un material a una fuerza estática o aplicada lentamente. Las velocidades de deformación en un ensayo de tracción suelen ser muy pequeñas (ε = 10–4 a 10–2 s–1).
Ensayos de compresión
En ingeniería, el ensayo de compresión es un ensayo técnico para determinar la resistencia de un material o su deformación ante un esfuerzo de compresión. En la mayoría de los casos se realiza con hormigones y metales (sobre todo aceros), aunque puede realizarse sobre cualquier material.
- Se suele usar en materiales frágiles.
- La resistencia en compresión de la mayoría de los materiales siempre es menor que en tracción, pero se presentan excepciones, por ejemplo el hormigón.
Se realiza preparando probetas normalizadas que se someten a compresión en una máquina universal.
Límite convencional de fluencia
El límite de fluencia significa el fin de la zona elástica del material y el inicio de la zona plástica. Eso significa que al superar el límite de fluencia, el material se deformará de forma permanente, irreversible.Ensayo de flexión
El ensayo de flexión se realiza en la máquina universal de ensayos, también empleada en otras pruebas como las de tracción, compresión y flexión. En este caso, es necesario cambiar los apoyos y el útil de carga. El ensayo consiste en someter una probeta, apoyada en los extremos, a una fuerza en su eje perpendicular.
Ensayo de dureza
Por lo general, un ensayo de dureza consiste en presionar un objeto (penetrador) con unas medidas y una carga concretos sobre la superficie del material a evaluar. La dureza se determina al medir la profundidad de penetración del penetrador o bien midiendo el tamaño de la impresión dejada por el penetrador.
Ensayo de fatiga
El ensayo de fatiga permite determinar la resistencia que ofrece una pieza ante cargas cíclicas.
La fatiga es la situación en la que se encuentran distintas piezas sometidas a cargas cíclicas cuya intensidad posee un valor inferior al crítico de rotura del material.
La amplitud de la tensión varía alrededor cuerpo de un valor medio, el promedio de las tensiones máxima y mínima en cada ciclo:
El intervalo de tensiones es la diferencia entre tensión máxima y mínima
Existen dos tipos de fatiga:
- Fatiga en elementos sin defectos: El comportamiento frente a la fatiga presentan la etapa de la nucleación de fisuras, y la etapa de crecimiento de las fisuras hasta alcanzar un tamaño crítico que originaría la rotura. Dos ejemplos de esta fatiga es el usado en bielas y ejes.
- Fatiga en elementos con defectos: La duración del elemento está limitada por la velocidad de crecimiento de las fisuras. Es necesario realizar análisis periódicos no destructivos, como ultrasonidos y radiografías. Varios ejemplos de esta fatiga es la que se produce en puentes, barcos y aviones. Resulta imposible garantizar la ausencia de defectos, ya que estos elementos se fabrican uniendo varias piezas, y en las uniones es inevitable que existan fisuras.
Cuando una pieza se encuentra sometida a un proceso de fatiga, las grietas de pequeño tamaño aumentan progresivamente hasta que se produce la rotura.
Ensayo Tecnológico
Los ensayos tecnológicos se utilizan para comprobar si un material es útil para una aplicación cuando no ha sido posible realizar comprobaciones tras los ensayos realizados.
Permiten solamente determinar si el material es útil o inútil para un propósito. Se empezaron a utilizar desde el momento en el que se comenzó la obtención y transformación de materiales. Se pretende representar las condiciones que va a sufrir el material, y depende de la forma geométrica del mismo.
Ensayo no destructivos
Se denomina ensayo no destructivo a cualquier tipo de prueba practicada a un material que no altere de forma permanente sus propiedades físicas, químicas, mecánicas o dimensionales. Los ensayos no destructivos implican un daño imperceptible o nulo. Los diferentes métodos se basan en la aplicación de fenómenos físicos tales como ondas electromagnéticas, acústicas, elásticas, emisión de partículas subatómicas, capilaridad, absorción y cualquier tipo de prueba que no implique un daño considerable a la muestra examinada.
Se identifican comúnmente con las siglas PND o NDT y se consideran sinónimos de ensayos no destructivos (END), inspecciones no destructivas, Pruebas no destructivas y exámenes no destructivos.
En general, los ensayos no destructivos proveen datos menos exactos acerca del estado de la variable a medir que los ensayos destructivos. Sin embargo, suelen ser más baratos para el propietario de la pieza a examinar, ya que no implican la destrucción de la misma. En ocasiones, los ensayos no destructivos buscan únicamente verificar la homogeneidad y continuidad del material analizado, por lo que se complementan con los datos provenientes de los ensayos destructivos
Líquidos permanentes
El ensayo de líquidos penetrantes para detectar defectos de rotura en la superficie de los materiales es uno de los métodos de ensayos no destructivos más utilizados y rentables.
Se trata de un método analítico no destructivo que sirve para detectar discontinuidades en las superficies de los materiales, como grietas, fracturas, porosidad, solapamientos o defectos en las juntas.
El ensayo de líquidos penetrantes se puede efectuar en cualquier material sólido no poroso, como en metales cerámicas o plásticos. Es muy habitual utilizarlo para detectar defectos en piezas fundidas, forjadas y soldadas, por ejemplo, para descubrir fallos en los ensayos de corrosión en los materiales. Además, es un test que se lleva a cabo en prácticamente cualquier sector industrial, como el energético, aeroespacial o petroquímico entre otros.
Partículas magnéticas
La inspección por partículas magnéticas es un tipo de ensayo no destructivo que permite detectar discontinuidades superficiales y subsuperficiales en materiales ferromagnéticos, que pueden dar lugar a futuras fallas de los mismos.
La aplicación del ensayo de Partículas Magnéticas consiste básicamente en magnetizar la pieza a inspeccionar, aplicar las partículas magnéticas (polvo fino de limaduras de hierro) y evaluar las indicaciones producidas por la agrupación de las partículas en ciertos puntos. Este proceso varía según los materiales que se usen, los defectos a buscar y las condiciones físicas del objeto de inspección.
Se utiliza cuando se requiere una inspección más rápida que la que se logra empleando líquidos penetrantes. Existen 32 variantes del método, y cada una sirve para diferentes aplicaciones y niveles de sensibilidad.
Este método se utiliza en materiales ferromagnéticos como el hierro, el cobalto y el níquel. Debido a su baja permeabilidad magnética, no se aplica ni en los materiales paramagnéticos (como el aluminio, el titanio o el platino) ni en los diamagnéticos (como el cobre, la plata, el estaño o el zinc).
Los defectos que se pueden detectar son únicamente aquellos que están en la superficie o a poca profundidad. Cuanto menor sea el tamaño del defecto, menor será la profundidad a la que podrá ser detectado.
Ultrasónico
Los ensayos de ultrasonidos sirven para identificar la presencia de posibles discontinuidades en la pieza a inspeccionar tanto superficiales como interiores. Utilizan la reflexión de las ondas acústicas para observar su comportamiento y sus ondas de reflexión. En función del comportamiento de las ondas se podrá detectar la presencia o no de las discontinuidades y su ubicación exacta.
Radiografía Industrial.
Hoy día, la radiografía industrial es uno de los métodos más utilizados en el control no destructivo de diferentes procesos de fabricación de piezas o componentes industriales. Este se basa en la interacción de ondas electromagnéticas de alta energía (rayos X o gamma) con la materia.
Estructura de los materiales.
Ciencia de los materiales
La ciencia de materiales es la disciplina científica encargada de investigar la relación entre la estructura y las propiedades de los materiales. Paralelamente, conviene matizar que la ingeniería de materiales se fundamenta en esta, las relaciones propiedades-estructura-procesamiento-funcionamiento, y diseña o proyecta alguna estructura posible del material, para conseguir un conjunto predeterminado de propiedades.
La ciencia de materiales es, por ello mismo, un campo multidisciplinario que estudia los conocimientos fundamentales sobre las propiedades físicas macroscópicas de los materiales y los aplica en varias áreas de la ciencia y la ingeniería, consiguiendo que estos puedan ser utilizados en obras, máquinas y herramientas diversas, o convertidos en productos necesarios o requeridos por la sociedad. Incluye elementos de la química y física, así como las ingenierías química, mecánica, civil, eléctrica, medicina, industrial, biología y ciencias ambientales. Con la atención de los medios puesta en la nanociencia y la nanotecnología en los últimos años, la ciencia de los materiales ha sido impulsada en muchas universidades.
A pesar de los espectaculares progresos en el conocimiento y en el desarrollo de los materiales en los últimos años, el permanente desafío tecnológico requiere materiales cada vez más sofisticados y especializados.
EI objeto de la Ciencia de Materiales.
El objeto de la Ciencia de Materiales es estudiar la relación entre la estructura de un material a nivel atómico y molecular y sus propiedades macroscópicas. Esto implica comprender cómo la disposición de los átomos y las moléculas en un material influye en sus propiedades físicas, químicas, mecánicas y térmicas.
Materiales para Ingeniería
Los materiales para Ingeniería son aquellos que se utilizan en la fabricación de componentes y productos para diversas aplicaciones en ingeniería. Estos materiales deben tener propiedades específicas que los hagan adecuados para resistir las condiciones a las que estarán expuestos, como cargas mecánicas, temperaturas extremas, corrosión, entre otros.
Tipos de Enlace
Los tipos de enlace en los materiales se refieren a las fuerzas que mantienen unidos a los átomos en una estructura. Los principales tipos de enlace son el iónico, donde los átomos comparten electrones de manera desigual; el covalente, donde los átomos comparten electrones de manera igual; y el metálico, donde los electrones están libres para moverse a través de la estructura.
Propiedades Mecánicas y Físicas de los Materiales
Las propiedades mecánicas y físicas de los materiales se refieren a las características que describen cómo un material responde a las fuerzas aplicadas sobre él. Las propiedades mecánicas incluyen la resistencia, la dureza, la elasticidad, la tenacidad y la ductilidad, mientras que las propiedades físicas incluyen la densidad, la conductividad térmica y eléctrica, la capacidad calorífica, entre otras.
Relación estructural y propiedades
La relación entre la estructura y las propiedades de los materiales se basa en el hecho de que la estructura atómica y molecular de un material determina en gran medida sus propiedades macroscópicas. Por ejemplo, la disposición de los átomos en un material cristalino influye en su resistencia mecánica y conductividad eléctrica.
EI problema de la elección de un material
El problema de la elección de un material se refiere a la decisión de seleccionar el material más adecuado para una aplicación específica. Esto implica considerar no solo las propiedades del material, sino también su disponibilidad, costos, procesabilidad y factores ambientales.
Estructura cristalina y amorfa
Las estructuras cristalinas tienen una disposición ordenada y periódica de átomos en una red tridimensional, mientras que las estructuras amorfas carecen de esta ordenación. Los materiales cristalinos suelen tener propiedades mecánicas y ópticas anisotrópicas, mientras que los amorfos suelen ser isotrópicos.
Estudio de las principales redes cristalinas
El estudio de las principales redes cristalinas se refiere a las estructuras básicas en las que se organizan los átomos en un cristal. Algunas de las redes más comunes son la cúbica, la hexagonal y la tetragonal, cada una con propiedades y simetrías características.
Índice de Miller Cristalográficos planos y dirección
El índice de Miller Cristalográficos se utiliza para describir planos y direcciones en un cristal. Estos índices son números enteros que representan la intersección de un plano con los ejes de coordenadas de un sistema cristalino.
Estudio de huecos en las redes.
El estudio de huecos en las redes cristalinas se refiere a los espacios vacíos o huecos que pueden existir entre los átomos en una red cristalina. Estos huecos pueden ser de diferentes tamaños y formas, y pueden afectar las propiedades del material.
Estructuras de materiales cerámicos sencillos
Las estructuras de materiales cerámicos sencillos se refieren a la organización atómica de los materiales cerámicos, que suelen tener enlaces iónicos y estructuras cristalinas. Estos materiales suelen ser duros y quebradizos, con altos puntos de fusión y baja conductividad eléctrica y térmica.
Estudio de la estructura amorfa.
El estudio de la estructura amorfa se refiere a la organización de los átomos en materiales amorfos, que carecen de una estructura cristalina ordenada. Estos materiales suelen ser más blandos y menos densos que los cristalinos, y suelen tener propiedades ópticas diferentes debido a la falta de orden en su estructura.
Imperfecciones cristalinas
Las imperfecciones cristalinas son defectos en la estructura cristalina de un material, que pueden ser de varios tipos:
- Vacantes: átomos que faltan en la red cristalina.
- Átomos intersticiales: átomos adicionales que se encuentran entre los sitios de la red.
- Dislocaciones: defectos lineales en la estructura cristalina.
- Impurezas: átomos de otros elementos que se encuentran en la red cristalina.
- Defectos de borde y de superficie: defectos en la estructura en los límites de grano y en la superficie del material.
Estas imperfecciones pueden afectar significativamente las propiedades mecánicas, eléctricas, ópticas y químicas de los materiales.
Defectos en la Red Cristalina
Los defectos en la red cristalina son irregularidades que alteran la estructura perfecta de un cristal. Estos defectos pueden influir significativamente en las propiedades mecánicas, eléctricas, térmicas y ópticas de los materiales. Se clasifican en imperfecciones puntuales, lineales y planas.
Imperfecciones Puntuales
Las imperfecciones puntuales son defectos que ocurren en uno o unos pocos átomos en la estructura cristalina. Los principales tipos son:
- Vacancias: Átomos que faltan en el lugar donde deberían estar.
- Intersticiales: Átomos adicionales que se ubican en posiciones intersticiales del cristal.
- Sustitucionales: Átomos de un elemento diferente que ocupan el lugar de átomos del cristal original.
Imperfecciones Lineales
Las imperfecciones lineales, o dislocaciones, son defectos que afectan una línea de átomos en el cristal. Existen dos tipos principales:
- Dislocaciones de borde: Ocurren cuando hay un semiplano extra de átomos en el cristal.
- Dislocaciones de tornillo: Se forman cuando hay un desplazamiento en espiral de planos atómicos debido a un esfuerzo cortante.
Propiedades Eléctricas y Magnéticas
Propiedades Eléctricas de los Materiales
- Resistividad y Conductividad: La resistividad mide la oposición al flujo de corriente eléctrica, mientras que la conductividad es su inverso.
- Constante Dieléctrica: Medida de la capacidad de un material para almacenar energía eléctrica en un campo eléctrico.
Bandas de Energía
- Banda de Valencia y Banda de Conducción: Las bandas de energía determinan la capacidad de los electrones para moverse a través del material.
- Brecha de Energía (Bandgap): Diferencia de energía entre la banda de valencia y la banda de conducción; esencial para entender conductores, semiconductores y aislantes.
Conductividad Eléctrica
- Conductores: Materiales con alta conductividad, como los metales.
- Semiconductores: Materiales con conductividad intermedia que puede ser modificada.
- Aislantes: Materiales con baja conductividad.
Estructura de Bandas Semiconductoras
- Intrínsecos: Semiconductores puros donde los electrones son excitados de la banda de valencia a la de conducción.
- Extrínsecos: Semiconductores dopados con impurezas que crean niveles de energía adicionales.
Semiconductores Intrínsecos
- Materiales puros como el silicio y el germanio.
- La conductividad depende de la temperatura.
Semiconductores Extrínsecos
- Tipo N: Dopados con elementos que tienen más electrones (donadores).
- Tipo P: Dopados con elementos que tienen menos electrones (aceptores).
Conceptos Generales del Magnetismo
- Momento Magnético: Propiedad de los electrones y átomos que contribuye al magnetismo.
- Campo Magnético: Región en la que una fuerza magnética puede ser detectada.
Tipos de Comportamiento Magnético
- Diamagnetismo: Materiales que crean un campo magnético opuesto al campo aplicado.
- Paramagnetismo: Materiales que se magnetizan débilmente en la dirección del campo aplicado.
- Ferromagnetismo: Materiales que se magnetizan fuertemente en la dirección del campo aplicado y mantienen la magnetización.
- Antiferromagnetismo: Materiales cuyos momentos magnéticos de átomos vecinos se alinean en direcciones opuestas.
- Ferrimagnetismo: Similar al antiferromagnetismo, pero los momentos magnéticos opuestos no son iguales y dejan una magnetización neta.
Materiales Magnéticos Duros y Blandos
- Materiales Magnéticos Duros: Mantienen su magnetización después de que se retira el campo magnético aplicado (e.g., imanes permanentes).
- Materiales Magnéticos Blandos: Pierden su magnetización fácilmente cuando se retira el campo magnético aplicado (e.g., núcleos de transformadores).
Comentarios
Publicar un comentario